A execução de um projeto exige planejamento, conhecimento técnico e uma boa gestão. No entanto, mesmo os projetistas e engenheiros mais experientes estão sujeitos a cometer erros que comprometem prazos, orçamentos e a qualidade final do produto. Neste artigo, você vai conhecer os 5 erros mais comuns em projetos e aprender como evitá-los com boas práticas.
1. Falta de Planejamento Detalhado
O planejamento é a espinha dorsal de qualquer projeto bem-sucedido. Quando essa etapa é negligenciada, os impactos negativos são inevitáveis: atrasos, estouros de orçamento, retrabalhos e insatisfação do cliente. Muitas empresas e profissionais subestimam o tempo necessário para planejar, preferindo partir rapidamente para a execução. Esse impulso pode ser custoso, principalmente em projetos de engenharia, onde cada detalhe influencia diretamente o desempenho do produto final.
Além disso, planejamentos superficiais ignoram riscos, limitações de recursos e prazos realistas, criando um efeito dominó de falhas operacionais.
Como evitar a falta de planejamento detalhado
1. Defina o escopo com clareza
Liste todos os requisitos técnicos, funcionais e operacionais do projeto. O escopo deve conter o que será entregue, como será entregue e quais não são responsabilidades da equipe de projeto.
2. Crie um cronograma estruturado
Utilize ferramentas como o diagrama de Gantt para organizar as atividades em sequência lógica e visualizar dependências. Isso ajuda a controlar prazos e identificar gargalos antecipadamente.
3. Realize o levantamento completo de recursos
Inclua:
- Mão de obra necessária;
- Equipamentos e ferramentas;
- Materiais;
- Custo estimado por fase.
4. Use metodologias e softwares de gestão de projetos
Ferramentas como MS Project, Trello, Asana ou Monday ajudam a acompanhar o andamento das tarefas e delegar responsabilidades com maior clareza.
5. Preveja riscos e cenários alternativos
Elabore uma análise de riscos contemplando:
- Riscos técnicos (ex: falha de material);
- Riscos financeiros (ex: variação cambial);
- Riscos operacionais (ex: atrasos de fornecedores).
Monte planos de contingência para mitigar os impactos.
2. Comunicação Ineficiente entre Equipes
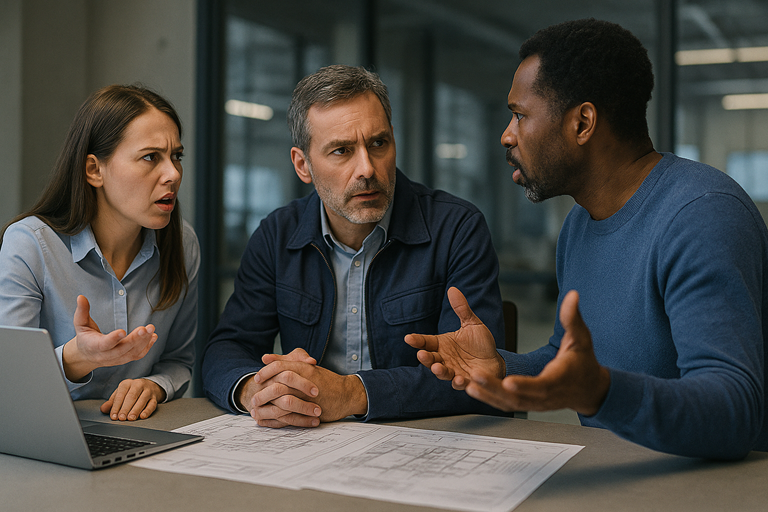
Por que é um erro?
A falha na comunicação entre os setores de projeto, produção e montagem pode gerar inconsistências nos desenhos técnicos, erros na fabricação e dúvidas na obra.
Como evitar:
- Estabeleça canais claros de comunicação (e-mails, reuniões semanais, ferramentas de colaboração como Slack ou Microsoft Teams);
- Registre todas as decisões e mudanças;
- Crie checklists de alinhamento entre as etapas do projeto.
3. Desconsiderar Tolerâncias e Condições Reais
Por que esse erro é tão crítico?
Projetar componentes sem considerar tolerâncias dimensionais, folgas adequadas e limitações dos processos de fabricação é um erro técnico grave. Na prática, isso pode levar à incompatibilidade entre peças, interferências durante a montagem ou falhas prematuras do equipamento.
Muitas vezes, o engenheiro foca apenas nas dimensões nominais e esquece que toda peça real sofre variações durante a fabricação, usinagem, conformação ou corte. Ignorar isso é assumir que todas as peças serão “perfeitas”, o que não condiz com a realidade industrial.
Além disso, o uso de tolerâncias inadequadas pode aumentar o custo de produção desnecessariamente, exigindo processos de alta precisão onde não há necessidade funcional.
Como evitar esse erro
1. Utilize tabelas de tolerância e ajustes normalizados
Adote sistemas como o ISO de Ajustes e Tolerâncias (ex: H7/g6, H8/f7, etc.) para definir os limites superior e inferior das dimensões. Isso garante intercambialidade e controle dimensional.
Você pode acessar a tabela de tolerância dimensional aqui.
Exemplo: Em vez de um furo “Ø50 mm”, especifique “Ø50 H7”, o que indica uma tolerância real para fabricação.
2. Considere os processos de fabricação e montagem
Cada processo tem sua capacidade de usinagem e margem de erro. Ao projetar, pense se a peça será fresada, estampada, cortada a laser ou fundida — e ajuste suas tolerâncias conforme o processo.
3. Aplique folgas funcionais e de montagem
Em conjuntos móveis (como mancais, polias, eixos e rolamentos), determine folgas de funcionamento e montagem, evitando interferências indesejadas.
4. Simule interferências no CAD
Use recursos de análise de interferência e jogo de folga em softwares como SolidWorks, Inventor ou Siemens NX para prever problemas antes da fabricação. Conheça Os Melhores Softwares para Engenharia Mecânica: Do CAD à Simulação
5. Documente as tolerâncias nos desenhos técnicos
Não deixe espaço para interpretações. Use cotas com tolerâncias bem definidas, conforme normas da ABNT ou ISO, e destaque cotas críticas nos detalhamentos.
4. Ignorar a Manutenção e o Pós-Venda
Projetos de engenharia que não consideram a manutenção e o suporte pós-venda tendem a apresentar custos operacionais elevados, insatisfação do cliente e falhas recorrentes ao longo da vida útil do equipamento. Esse é um erro comum entre engenheiros que focam apenas no funcionamento inicial do produto, sem pensar na manutenibilidade, desmontagem e suporte técnico futuro.
Ao ignorar essa etapa, o projeto se torna caro de manter, difícil de reparar e — em muitos casos — exige paradas totais para manutenções simples, o que é inaceitável em ambientes industriais ou agrícolas.
Além disso, o pós-venda é uma extensão estratégica do projeto, sendo essencial para fidelizar clientes, coletar feedbacks e melhorar versões futuras do produto.
Como evitar esse erro de projeto
1. Projete com foco na manutenção preventiva
Inclua sensores de monitoramento, interfaces acessíveis, conexões rápidas e peças padronizadas. Isso facilita intervenções e reduz o custo de operação.
2. Crie manuais técnicos claros e completos
Documente:
- Esquemas de montagem e desmontagem;
- Planos de manutenção periódica;
- Procedimentos de segurança e ajustes;
- Lista de peças de reposição.
3. Implemente um plano de pós-venda estruturado
- Treine equipes de campo ou o cliente final;
- Ofereça suporte técnico e consultoria remota;
- Acompanhe a performance do equipamento nas primeiras semanas;
- Estabeleça canais de atendimento (telefone, e-mail, WhatsApp, portal técnico).
4. Colete feedback técnico para melhorias
Após a entrega, obtenha retorno do cliente e equipe de campo. Use esses dados para corrigir falhas e aplicar melhoria contínua nos próximos projetos.
Não Aprender com Projetos Anteriores
Um dos erros mais negligenciados em projetos é ignorar a análise crítica dos projetos anteriores. Muitos profissionais e empresas avançam de um projeto para outro sem documentar os acertos, os erros e os pontos de melhoria. O resultado? Os mesmos problemas se repetem: atrasos, falhas técnicas, retrabalho, insatisfação do cliente — tudo por falta de aprendizado organizacional.
A engenharia moderna exige um ciclo de melhoria contínua, com base na coleta e análise de dados reais, pós-obra ou pós-entrega. Aprender com os erros — e também com os acertos — é essencial para ganhar eficiência, reduzir riscos e aumentar a competitividade no mercado.
Como evitar esse erro
Para evitar o erro de não aprender com projetos anteriores, é fundamental implementar uma cultura de melhoria contínua e gestão do conhecimento. Isso começa com a documentação sistemática das lições aprendidas — tanto os acertos quanto os erros — em uma base acessível a toda a equipe. Reuniões de encerramento (post-mortem) ao final de cada projeto ajudam a levantar insights valiosos sobre o que funcionou, o que precisa ser corrigido e como evitar falhas futuras. Além disso, o uso de indicadores de desempenho (KPIs) permite monitorar a eficiência dos projetos ao longo do tempo e identificar padrões de falhas recorrentes.
Também é essencial transformar boas práticas em processos padronizados para projetos futuros, além de promover o compartilhamento de conhecimento entre os membros da equipe. Criar um ambiente onde os profissionais se sintam encorajados a registrar, relatar e propor melhorias técnicas fortalece a qualidade dos próximos projetos e reduz significativamente retrabalhos e desperdícios. Dessa forma, cada projeto se torna não apenas uma entrega, mas uma oportunidade de evolução técnica e organizacional.